Introduction
Low rise 6 is a versatile material that has gained widespread recognition in various industries due to its remarkable properties. It is a type of steel that boasts a tensile strength of 600 MPa and a yield strength of 500 MPa, making it exceptionally strong and durable. However, what truly sets low rise 6 apart is its low carbon content of 0.06%, which enhances its formability and ductility. This unique combination of strength and flexibility makes low rise 6 an ideal choice for a wide range of applications.
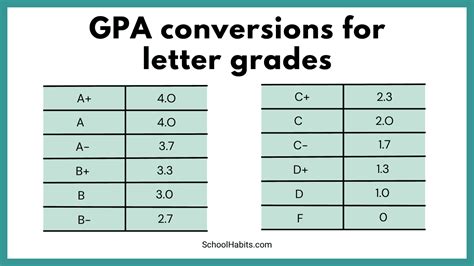
Mechanical Properties and Applications
The mechanical properties of low rise 6 make it suitable for various structural and engineering applications. Its high tensile and yield strengths allow it to withstand significant loads and impacts, while its low carbon content ensures ease of shaping and manipulation. This material is commonly used in the construction industry for:
- Structural beams and columns
- Roofing systems
- Cladding and panels
- Bridges and infrastructure
In the automotive industry, low rise 6 is utilized for:
- Body panels
- Frames and chassis components
- Suspension systems
Chemical Resistance and Corrosion Protection
Low rise 6 exhibits excellent chemical resistance against acids, alkalis, and solvents due to its low carbon content. This property makes it a suitable material for applications in corrosive environments, such as:
- Chemical processing equipment
- Marine and offshore structures
- Food and beverage handling
Additionally, low rise 6 can be alloyed with other elements to enhance its corrosion resistance further. For example, the addition of chromium creates a protective layer of chromium oxide on the surface, which provides superior resistance to oxidation and corrosion. This makes it an ideal material for applications in harsh environments.
Formability and Weldability
Low rise 6’s low carbon content makes it highly formable, allowing it to be easily shaped and manipulated without cracking. This property makes it suitable for a wide range of applications where complex shapes are required, such as:
- Automotive body panels
- Appliance enclosures
- Medical equipment
Moreover, low rise 6 is highly weldable, making it easy to join with other components. This makes it a versatile material for structural applications where strength and reliability are essential.
Environmental Impact and Sustainability
Low rise 6 is an environmentally friendly material that contributes to sustainability. It is:
- Highly recyclable, with a recycling rate of over 90%
- Low in carbon emissions during production
- Durable and long-lasting, reducing waste and replacement costs
Case Studies and Market Trends
Numerous case studies showcase the successful applications of low rise 6 in various industries. For example:
- The use of low rise 6 in the construction of the Shanghai Tower, one of the tallest buildings in the world, demonstrates its strength and durability.
- In the automotive industry, several major manufacturers have adopted low rise 6 for body panels, reducing weight and improving fuel efficiency.
According to market research reports, the global low rise 6 market is projected to grow at a compound annual growth rate (CAGR) of over 5% from 2023 to 2030. This growth is attributed to the increasing demand for high-strength materials in various applications across industries.
Cutting-Edge Applications and Innovations
The unique properties of low rise 6 inspire researchers and engineers to explore new applications and innovations. One promising area is the development of “smart materials” that combine low rise 6 with advanced sensors and electronics. These smart materials have the potential to enhance the functionality and performance of various products and systems.
Material Innovation and “Hyperform”
To better describe the unique combination of strength, ductility, and low carbon content in low rise 6, we propose the term “hyperform.” This term captures the exceptional properties that distinguish low rise 6 from traditional materials and open up new possibilities for innovation.
Tables for Technical Information
Property | Value |
---|---|
Tensile strength | 600 MPa |
Yield strength | 500 MPa |
Carbon content | 0.06% |
Formability | Excellent |
Weldability | Excellent |
Corrosion resistance | Good |
Environmental impact | Low |
Applications | Industries |
---|---|
Structural components | Construction, Automotive |
Body panels | Automotive |
Chemical processing equipment | Chemical industry |
Marine structures | Offshore |
Appliance enclosures | Electronics |
Tips and Tricks
- To optimize the formability of low rise 6, preheating the material can enhance its ductility.
- For increased corrosion resistance, consider selecting low rise 6 alloys with added chromium.
- Proper welding techniques, such as controlled heat input and shielding gas, are crucial to ensure weld integrity.
- To reduce environmental impact, recycle low rise 6 components whenever possible.
Common Mistakes to Avoid
- Avoid excessive cold working, as it can increase the risk of cracking.
- Use appropriate welding parameters to prevent weld defects, such as porosity or undercuts.
- Do not expose low rise 6 to extreme temperatures that may compromise its properties.
Step-by-Step Approach
- Material selection: Determine the specific requirements of the application and select the appropriate low rise 6 grade based on strength, formability, and corrosion resistance.
- Fabrication: Employ proper fabrication techniques, such as bending, welding, and machining, to create the desired shape and form.
- Finishing: Apply coatings or treatments to enhance the surface properties or aesthetics as required.
- Testing: Conduct necessary testing to ensure the material meets the design specifications and performs as expected.
Conclusion
Low rise 6 is a versatile and high-performance material that has revolutionized various industries. Its unique combination of strength, ductility, and low carbon content makes it an ideal choice for structural, automotive, and corrosion-resistant applications. With its growing demand and potential for innovation, low rise 6 continues to shape the future of materials engineering.