Introduction
Tom P. Haney, a visionary leader in the manufacturing industry, has made groundbreaking contributions that have transformed the way products are designed, produced, and delivered. His innovative ideas and relentless pursuit of excellence have shaped the future of manufacturing, ushering in an era of efficiency, sustainability, and customer satisfaction.
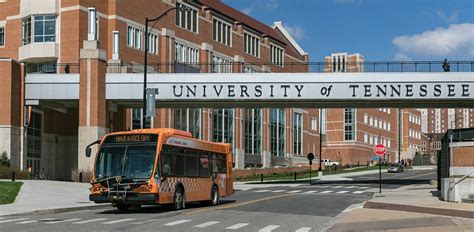
Haney’s Key Contributions
1. Lean Manufacturing Principles
Haney is widely recognized as the co-developer of the Toyota Production System (TPS), a set of lean manufacturing principles that revolutionized the automotive industry and spread to other sectors. TPS focuses on eliminating waste, streamlining processes, and improving quality. As a result, companies that implement TPS experience significant reductions in lead times, inventory, and defects.
2. Supply Chain Management
Haney played a pivotal role in developing modern supply chain management practices. He emphasized the importance of collaboration between suppliers, manufacturers, and customers to reduce costs, improve efficiency, and ensure the timely delivery of quality products. His insights have led to the creation of global supply chains that enable manufacturers to access raw materials and components from around the world.
3. Kaizen Philosophy
Haney introduced the Kaizen philosophy, a continuous improvement approach that encourages employees at all levels to identify and eliminate inefficiencies. By fostering a culture of continuous learning and problem-solving, Kaizen helps organizations achieve incremental but sustained improvements in quality, productivity, and profitability.
Haney’s Legacy and Impact
1. Global Impact
Haney’s ideas have had a profound impact on manufacturing industries worldwide. His lean manufacturing principles and supply chain management practices have become essential elements of modern production systems. Companies that embrace these principles have achieved significant competitive advantages, leading to increased market share and profitability.
2. Workforce Development
Haney recognized the importance of skilled workforce in manufacturing. He advocated for the development of training programs and educational initiatives to equip workers with the knowledge and skills necessary to operate lean manufacturing systems. His efforts have helped create a highly skilled and adaptable workforce that supports the growth and innovation of the manufacturing industry.
3. Sustainability
Haney’s focus on waste reduction aligns with the principles of sustainability. Lean manufacturing practices minimize energy consumption, reduce emissions, and conserve resources. By applying lean principles, manufacturers can contribute to environmental protection while also improving their bottom line.
Table 1: Benefits of Lean Manufacturing
Benefit | Impact |
---|---|
Reduced waste | Lower production costs |
Improved efficiency | Increased productivity |
Enhanced quality | Reduced defects |
Shorter lead times | Faster delivery to customers |
Reduced inventory | Lower storage costs |
Table 2: Common Mistakes to Avoid in Implementing Lean Manufacturing
Mistake | Consequence |
---|---|
Lack of employee involvement | Resistance to change and suboptimal implementation |
Overfocus on cost cutting | Compromised quality and productivity |
Inconsistent implementation | Inadequate results and wasted effort |
Lack of metrics and tracking | Difficulty in measuring progress and making improvements |
Failure to adopt a long-term perspective | Short-term gains that do not sustain over time |
Table 3: Haney’s Key Innovations
Innovation | Impact |
---|---|
Toyota Production System | Revolutionized automotive manufacturing |
Kaizen philosophy | Fostered continuous improvement |
Just-in-time manufacturing | Reduced inventory and waste |
Single-piece flow | Improved efficiency and quality |
Kanban system | Visualized inventory and production schedules |
Table 4: Applications of Lean Manufacturing Principles
Industry | Result |
---|---|
Automotive | Reduced defects, increased productivity |
Healthcare | Improved patient care, reduced costs |
Aerospace | Enhanced safety and reliability |
Electronics | Decreased lead times, improved quality |
Retail | Optimized inventory levels, reduced waste |
A New Word for Innovation: “Kaidapt”
To generate ideas for new applications of lean manufacturing principles, consider the term “Kaidapt.” This word combines “Kaizen” (continuous improvement) with “adapt” (adjusting to changing conditions). “Kaidapt” suggests exploring new ways to adapt lean principles to different industries and contexts, fostering innovation and enhancing manufacturing practices.
Step-by-Step Approach to Implementing Lean Manufacturing
1. Identify Waste
Conduct a thorough analysis to identify areas of waste and inefficiency in your production process. Consider muda (waste) categories such as overproduction, waiting, transportation, overprocessing, inventory, and defects.
2. Create a Value Stream Map
Map the flow of materials and information through your production process. Identify bottlenecks, delays, and areas for improvement.
3. Implement Kaizen Practices
Empower employees to identify and eliminate inefficiencies at all levels. Encourage suggestions and provide training on Kaizen tools and techniques.
4. Embrace a Just-in-Time Approach
Reduce inventory levels and improve supply chain collaboration to eliminate waste and improve efficiency.
5. Monitor and Evaluate
Establish metrics to track progress and identify areas for further improvement. Conduct regular audits to ensure continuous improvement efforts are sustained.
Why Lean Manufacturing Matters
1. Customer Focus
Lean manufacturing emphasizes customer satisfaction by delivering high-quality products on time and at a competitive price.
2. Increased Productivity
By eliminating waste and improving efficiency, lean manufacturing principles can significantly increase productivity and reduce production costs.
3. Competitive Advantage
Companies that effectively implement lean manufacturing gain a competitive advantage by producing products faster, better, and at a lower cost.
4. Environmental Sustainability
Lean manufacturing practices reduce waste, energy consumption, and emissions, contributing to environmental protection.
5. Employee Engagement
Kaizen philosophy fosters a culture of continuous improvement and employee engagement, leading to higher morale and increased retention rates.
Conclusion
Tom P. Haney’s contributions to manufacturing have had a transformative impact on industries worldwide. His lean manufacturing principles, supply chain management practices, and Kaizen philosophy have empowered organizations to achieve greater efficiency, profitability, and sustainability. As manufacturing continues to evolve, Haney’s legacy will continue to inspire innovation and drive progress towards a more efficient, customer-centric, and environmentally responsible future.