Robin Bullock, a renowned futurist and author, proposed a comprehensive framework in Chapter 14 of his book “The Six Sigma Revolution” that serves as a roadmap for organizations to achieve operational excellence. This chapter provides a systematic approach to improving processes, reducing defects, and enhancing overall performance.
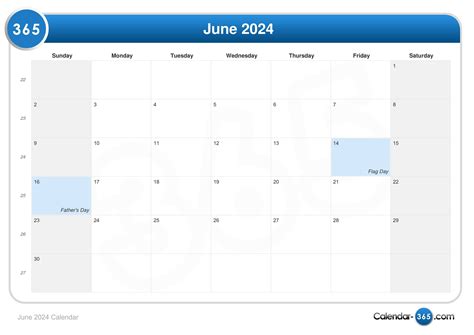
The FOCUS-PDCA Cycle
Bullock’s framework revolves around the FOCUS-PDCA cycle, an iterative process that encapsulates the key steps involved in continuous improvement:
- Find: Identify areas for improvement and gather data to quantify the problem.
- Organize: Establish a team and clarify roles, responsibilities, and expectations.
- Clarify: Develop a clear understanding of the problem and its root causes.
- Understand: Analyze the data and identify specific solutions to address the problem.
- Select: Choose the best solution and develop an implementation plan.
- Plan: Prepare detailed instructions and resources for implementing the solution.
- Do: Execute the solution and monitor its progress closely.
- Check: Evaluate the effectiveness of the solution and make adjustments as needed.
- Act: Standardize the successful solution and implement it throughout the organization.
Key Metrics and Tools
Bullock emphasizes the use of key metrics to track progress and measure improvement. These metrics include:
- Defects per Million Opportunities (DPMO): A measure of the number of defects detected per million opportunities for a process to generate defects.
- Process Capability Index (Cp/Cpk): A measure of the process capability relative to customer specifications.
- Return on Investment (ROI): A measure of the financial benefits realized from a Six Sigma project.
Bullock also advocates for the use of various tools, such as:
- Failure Mode and Effects Analysis (FMEA): A tool to identify potential failure modes of a process and their consequences.
- Statistical Process Control (SPC): A tool to monitor and control processes using statistical techniques.
- Design of Experiments (DOE): A tool to optimize processes by systematically varying inputs and measuring outputs.
Benefits of the FOCUS-PDCA Cycle
Adopting the FOCUS-PDCA cycle offers numerous benefits to organizations, including:
- Reduced defects and improved quality: By identifying and eliminating root causes of problems, organizations can significantly reduce defects and enhance product and service quality.
- Increased productivity and efficiency: Optimized processes lead to increased productivity, faster turnaround times, and reduced waste.
- Enhanced customer satisfaction: Improved quality and efficiency directly contribute to improved customer satisfaction and loyalty.
- Lower costs: By reducing defects, organizations can minimize rework, scrap, and warranty claims, leading to lower operating costs.
Comparative Analysis of Pros and Cons
Pros | Cons |
---|---|
Systematic and comprehensive approach | Time-consuming and resource-intensive |
Proven track record of success | Requires a strong commitment from leadership |
Improves operational performance | May not be suitable for all situations |
Reduces defects and costs | Can be difficult to implement effectively |
Enhances customer satisfaction | Requires continuous monitoring and improvement |
Provides a framework for continuous improvement | May encounter resistance from employees |
Frequently Asked Questions
Q: What are the key components of Robin Bullock’s FOCUS-PDCA cycle?
A: Find, Organize, Clarify, Understand, Select, Plan, Do, Check, Act.
Q: What are the primary benefits of implementing the FOCUS-PDCA cycle?
A: Reduced defects, improved quality, increased productivity, enhanced customer satisfaction, and lower costs.
Q: How can I measure the effectiveness of a Six Sigma project?
A: Use metrics such as DPMO, Cp/Cpk, and ROI to quantify improvements.
Q: What tools can I use to implement the FOCUS-PDCA cycle?
A: FMEA, SPC, and DOE are effective tools for identifying and eliminating root causes of problems and optimizing processes.
Q: How long does it take to implement the FOCUS-PDCA cycle?
A: The duration varies depending on project complexity and organizational size, but it typically takes several months to achieve significant results.
Q: Who is responsible for implementing the FOCUS-PDCA cycle?
A: A cross-functional team led by a Six Sigma Champion is typically responsible for implementing and sustaining improvements.
Q: How can I ensure the sustainability of Six Sigma improvements?
A: Continuous monitoring, employee training, and ongoing project management are key to maintaining and expanding Six Sigma gains.
Q: What industries are best suited for Six Sigma implementation?
A: Six Sigma can be applied to any industry or organization seeking to improve processes, reduce defects, and enhance performance.