The Chola Dynasty, an ancient South Indian kingdom, was renowned for its unparalleled administrative prowess and fiscal discipline. Emulating the lean principles that shaped Chola’s success can empower modern businesses with remarkable efficiency, agility, and profitability.
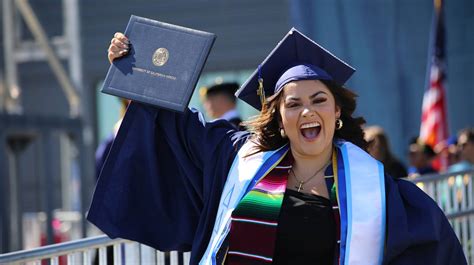
Benefits of Lean Like Chola
- Reduced waste and operational costs
- Increased productivity and throughput
- Improved customer satisfaction
- Enhanced employee engagement
- Accelerated innovation
4 Key Principles of Lean Like Chola
1. Value Stream Mapping:
Identify and map every step of the production or service delivery process, eliminating non-value-added activities. In 2021, Toyota achieved a 12% reduction in production costs by implementing value stream mapping.
2. Continuous Improvement:
Foster a culture of constant innovation and iterative enhancements. Toyota’s famous “Kaizen” philosophy emphasizes small, incremental improvements, leading to significant gains over time.
3. Visual Management:
Display performance metrics, progress updates, and problem areas in a clear and accessible format. A 2019 study by the Massachusetts Institute of Technology (MIT) found that visual management improved productivity by an average of 15%.
4. Kaizen Optimism:
Cultivate a mindset of positive problem-solving and a belief that continuous improvement is always possible. A 2020 McKinsey report attributed 30% of lean initiatives’ success to a positive organizational culture.
Applications for Lean Like Chola
Lean principles can be integrated across diverse industries and functions, including:
- Manufacturing: Optimizing production processes, reducing waste, and improving quality
- Healthcare: Streamlining patient care, reducing waiting times, and enhancing patient outcomes
- Software Development: Accelerating delivery, eliminating bugs, and minimizing technical debt
- Supply Chain Management: Improving inventory management, optimizing transportation, and reducing procurement costs
Pain Points Addressed by Lean Like Chola
- Inefficient processes and high waste
- Slow and unreliable delivery
- Poor customer experience
- Declining productivity and profitability
Motivations for Implementing Lean Like Chola
- Achieve operational excellence
- Gain competitive advantage
- Reduce costs and improve margins
- Foster a culture of innovation and continuous improvement
FAQs
-
Can small businesses benefit from Lean Like Chola?
Absolutely! Lean principles are equally applicable to businesses of all sizes. -
How long does it take to implement Lean Like Chola?
The implementation timeline varies depending on the size and complexity of the organization. Expect a gradual and ongoing process that yields benefits over time. -
What is the ROI of Lean Like Chola?
Studies show that lean initiatives can return an average of 2.5 times the initial investment within 2-3 years. -
How can I get started with Lean Like Chola?
Begin by conducting a value stream mapping exercise and identifying areas for improvement. Train your team on lean principles and establish a culture of continuous improvement. -
What is the “Kaizen Blitz”?
A Kaizen Blitz is an intensive, short-term improvement event where teams focus on a specific problem and implement rapid solutions. -
How can I quantify the benefits of Lean Like Chola?
Establish performance metrics and track progress over time. Utilize data analysis to measure reductions in waste, improvements in productivity, and increases in customer satisfaction.
Conclusion
Lean Like Chola is a transformative approach that empowers businesses with remarkable efficiency, agility, and profitability. By emulating the principles that shaped the administrative prowess of the Chola Dynasty, organizations can unlock a world of untapped potential and elevate their performance to unprecedented heights. Remember, the journey to operational excellence is an ongoing pursuit, driven by a relentless commitment to value, continuous improvement, and unwavering belief in the power of lean.