3D manufacturing (3 2 M) is fundamentally changing the way industries design, manufacture, and deliver products. This transformative technology enables the creation of complex and customized products with unprecedented speed, efficiency, and cost savings.
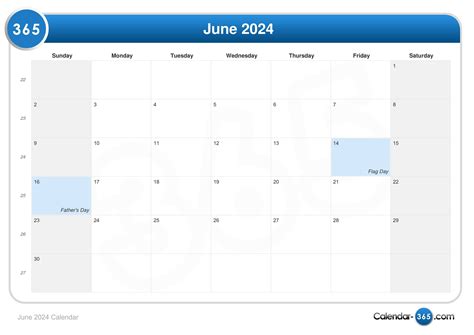
The Rise of 3 2 M
According to the American Society of Mechanical Engineers (ASME), the global 3D manufacturing market is projected to reach $13.8 billion by 2028, with a compound annual growth rate (CAGR) of 14.2%. This rapid growth is driven by advancements in 3D printing technologies, materials, and software, as well as the increasing demand for personalized and customized products.
Applications of 3 2 M
The applications of 3 2 M span a wide range of industries, including:
- Manufacturing: Creation of prototypes, molds, and tooling; production of complex and customized parts
- Healthcare: Fabrication of medical devices, prosthetics, and dental implants
- Aerospace: Design and production of lightweight and durable aircraft components
- Automotive: Prototyping and testing of vehicles; manufacturing of custom parts
- Consumer Products: Production of personalized jewelry, toys, and home décor
Benefits of 3 2 M
The adoption of 3 2 M offers numerous benefits, including:
- Reduced Production Costs: Eliminate the need for traditional tooling and allow for cost-effective production of prototypes and small batches.
- Faster Time-to-Market: Rapidly create prototypes and iterate on designs, reducing development time and speeding up product launches.
- Increased Design Flexibility: Enable the creation of complex and customized products with intricate geometries that are not feasible with traditional manufacturing methods.
- Improved Supply Chain Efficiency: Decentralize production and reduce reliance on overseas manufacturing, minimizing lead times and improving responsiveness to market demand.
- Environmental Sustainability: Reduce waste and material consumption through additive manufacturing techniques that only use the necessary materials.
Strategies for Successful Implementation
Successful implementation of 3 2 M requires a well-defined strategy that addresses the following aspects:
- Technology Selection: Choose the appropriate 3D printing technology and materials based on the specific application requirements.
- Workforce Training: Invest in training and upskilling employees to develop the necessary technical skills and knowledge for 3D manufacturing.
- Process Optimization: Streamline the 3D printing process to maximize efficiency, reduce downtime, and improve quality control.
- Design for 3D Manufacturing: Implement design principles that leverage the unique capabilities of 3D printing, such as biomimicry and topology optimization.
- Quality Assurance: Establish robust quality control measures to ensure the reliability and consistency of 3D printed parts.
Common Mistakes to Avoid
To avoid common pitfalls in 3D manufacturing, businesses should adhere to the following best practices:
- Overestimating Capabilities: Do not assume that all designs are suitable for 3D printing. Carefully evaluate the limitations of the technology and design accordingly.
- Ignoring Material Properties: Understand the mechanical and functional properties of different 3D printing materials to select the most appropriate one for each application.
- Neglecting Post-Processing: Recognize that most 3D printed parts require post-processing, such as sanding, finishing, and heat treatment, to achieve optimal results.
- Failing to Integrate with Supply Chain: Consider the impact of 3D manufacturing on the entire supply chain, including inventory management and distribution channels.
- Overlooking Safety: Ensure proper ventilation and follow safety guidelines when using 3D printing technologies to minimize exposure to hazardous fumes and particles.
Conclusion
3 2 M is a revolutionary technology with the potential to transform industries and create new possibilities for innovation. By understanding its benefits, strategies, and potential pitfalls, businesses can leverage 3D manufacturing to improve product quality, reduce costs, and gain a competitive advantage in the global marketplace.
Table 1: 3D Printing Technologies
Technology | Description | Advantages | Disadvantages |
---|---|---|---|
Fused Deposition Modeling (FDM) | Layer-by-layer deposition of thermoplastic materials | Low cost, ease of use | Limited resolution, slow build times |
Stereolithography (SLA) | Photopolymerization of liquid resins using UV light | High resolution, smooth surface finish | Expensive materials, complex post-processing |
Selective Laser Sintering (SLS) | Sintering of powdered materials using a laser | Durable parts, complex geometries | High material costs, requires post-processing |
Metal 3D Printing | Additive manufacturing of metal parts using laser or electron beam melting | High strength, durability | Expensive equipment, limited material options |
Table 2: Applications of 3D Manufacturing
Industry | Applications | Benefits |
---|---|---|
Healthcare | Medical devices, prosthetics, tissue engineering | Personalized and optimized devices, reduced patient recovery time |
Aerospace | Aircraft components, engine parts | Lightweight and durable designs, reduced production costs |
Automotive | Prototyping, custom parts | Faster design iterations, cost savings on low-volume production |
Consumer Products | Jewelry, toys, home décor | Personalized designs, shorter lead times |
Table 3: Strategies for Successful 3D Manufacturing Implementation
Strategy | Description | Benefits |
---|---|---|
Technology Selection | Choose the right 3D printing technology and materials for the application | Optimal part quality, efficiency, and cost-effectiveness |
Workforce Training | Upskill employees on 3D manufacturing techniques | Improved technical knowledge, reduced downtime |
Process Optimization | Streamline the 3D printing process | Increased efficiency, reduced lead times |
Design for 3D Manufacturing | Implement design principles that leverage 3D printing capabilities | Complex and optimized designs, reduced material waste |
Quality Assurance | Establish robust quality control measures | Reliable and consistent part quality |
Table 4: Common Mistakes to Avoid in 3D Manufacturing
Mistake | Description | Consequences |
---|---|---|
Overestimating Capabilities | Assuming all designs are suitable for 3D printing | Poor part quality, failed builds |
Ignoring Material Properties | Not understanding the mechanical and functional properties of materials | Compromised part performance |
Negating Post-Processing | Overlooking the need for post-processing steps | Reduced part quality, increased downtime |
Failing to Integrate with Supply Chain | Ignoring the impact of 3D manufacturing on the supply chain | Production delays, inventory challenges |
Overlooking Safety | Neglecting proper ventilation and safety guidelines | Health and safety hazards |